History
1983-1988 Concept
The Negative Pressure Supercharging concept was first conceived 1983 in Sydney
Australia by Alexander Chabry, a 21 year old self-taught engineer with a remarkable
insight into the fluid dynamics of the conventional 4-stroke engine. He was inspired by
the fast acceleration produced by the low revving 225 Chrysler slant 6 and the massive
towing power (torque) produced by heavy trucks. He figured cars could use low rpm torque
instead of high rpm horsepower to substantially improve acceleration and fuel economy.
Alex explored this
new supercharging concept for over 5 years to work out its basic operating principles
before he applied it to the 4-stroke engine. Although the concept is radically different
to conventional principles, he knew it will work because the idea is based on sound
physics. He was proven right in 1997 when the Negative Pressure Supercharging concept
became a working reality. But what Alex didn't know is that it will take more than 15
years to figure out the complex fluid dynamics of Negative Pressure Supercharging to make
it work in the 4-stroke engine.
It's interesting to note that in 1876 the inventor of the 4-stroke engine was not the
steam locomotive companies but instead Nicolaus August Otto a brilliant self-taught
engineer. The situation is the same today. Its not car companies that have invented this
revolutionary new supercharging process that makes the 4-stroke engine supercharge itself
using NO air pump but again a brilliant self-taught engineer, Alexander Chabry.
Top of page
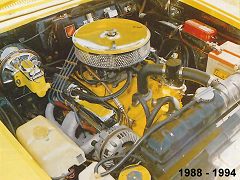
1988-1993 Development
Development of the Negative Pressure Supercharging concept began in October 1988 on an
early 360ci Chrysler small block that was fully rebuilt using standard parts and the
Negative Pressure Supercharging headers, valve timing, ignition timing and modified heads
and intake manifold.
The mechanically simple design of the 360 allowed us to go back to basics in order to
develop the complex fluid dynamics of this new supercharging process and the heavy duty
construction of the 360 allowed the engine to operate reliably for 17 years and 50,000
miles (80,000 km) of extensive testing with no failure to any engine parts. However, over
the 17 years the 360 broke 3 torque converters and 1 flex band in the transmission due to
the massive torque produced by the Negative Pressure Supercharging process.
We chose a standard
1972 360 Chrysler small block to develop this new supercharging concept because it's a
mechanically simple heavy duty pushrod engine that features a number of remarkable
technological advancements not found on other more popular thin wall construction V8's
produced over the past 30 years such as,
- stronger thick wall construction block and heads,
- larger cylinder head and crank main end bolts,
- heavy duty rocker shaft valve train,
- high flow 23° intake ports,
- valves that open at the centre of the cylinder to minimise valve shrouding and increase
air flow,
- larger diameter and taller valve springs that allow more lift and higher spring
pressures with fast acting cams,
- centrally located spark plugs in combustion chamber that produce a superior burn and
more power,
- wider diameter camshaft that minimises cam flex and optimises valve timing,
- larger diameter cam lifters (tappets) that allow more valve lift and much faster opening
valves to increase air flow and produce more power,
- camshaft thrust plate that prevents cam walk and damage to cam lobes, lifters (tappets)
and timing chain,
- stronger crankshaft with larger bearings to handle high torque loads,
- stronger piston pins with a larger diameter to handle high torque loads,
- larger heavy duty con-rods to handle high torque loads,
- higher crank to con-rod ratio that produces more torque,
- electronic ignition distributor with heavy advance weights that stabilise ignition
timing and eliminate spark scatter.
Over the next 5 years development of the Negative Pressure Supercharging process
involved extensive trial and error testing of hundreds of different combinations,
increasing the speed of the exhaust gas from the common 300 ft/sec to a faster 450 ft/sec,
advancing the valve timing events, using radical ignition advance curves and a compact
megaphone Tri-Y exhaust header with small pipes half the size and one third the length of
conventional headers. By mid 1993 a portion of the Negative Pressure Supercharging concept
began to work for the first time and it was no longer a concept. During 1993 we also
established Patents worldwide as the inventor of the Negative Pressure Supercharging
technology.
Top of page
1993-1995 Development
The huge increase in torque produced by the Negative Pressure Supercharging process,
encouraged us to use even smaller diameter header pipes in order to produce a higher gas
speed. As a result, the gas velocity was twice the speed produced by conventional headers.
However, the higher gas velocity changed the optimum fluid dynamics (air and gas flow) and
prevented this supercharging process from working.
After 2 years of trial and error testing, we found that when the speed of the exhaust gas
was increased in the header from 450 ft/sec to a much faster 600 ft/sec, even less exhaust
valve lift and overlap duration is required and 4 key areas of the engine that control the
fluid dynamics (air and gas flow) need to be synchronised together for the Negative
Pressure Supercharging process to work. This was an exciting breakthrough. It would have
been almost impossible to figure out how this new supercharging process works if we had
not discovered that several unique valve timing events need to work in synch.
Top of page
1995-1997 Development to Success
We continued to test many other different combinations and to refine the Negative
Pressure Supercharging process with this new information. We found a total of 8 key areas
of the camshaft, cylinder head and exhaust header need to be synchronised together for
this new supercharging process to work at optimum and increase the supercharging effect.
On 10 December 1997 the Negative Pressure Supercharging process officially became
a working reality.
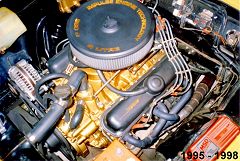
We approached a number of car makers around the world to see if they were interested in
the Negative Pressure Supercharging technology and found a disturbing trend. Car makers
are not interested in any new engine technology that comes from outside their company even
if it's more advanced and cost-effective to produce. Car makers would rather make new car
engines more mechanically complex each year using their own technology to improve
performance than pay for highly advanced technology that originates outside their company.
We were disappointed but it did not worry us that car makers have closed their doors to
new engine technology. New cars are a very small market and Negative Pressure
Supercharging can be applied to the 700 million engines currently being used worldwide in
cars, pickups, RV's, trucks, buses, motorcycles, boats, tractors to propeller planes
produced from 1900 to the present time.
Top of page
1997-1999 Refinement
We made further refinements and found the Negative Pressure Supercharging process also
requires hot air induction and a cold water temperature to work at optimum and increase
the supercharging effect. However, due to the many inquiries we received for Negative
Supercharging Kits we gradually stopped most of the development and focused our resources
to tooling up to produce Kits.
Top of page
1999-2002 Tooling Up
During this
period we set up the tooling to produce the special parts of the Negative Supercharging
Kits for initially 318 360 Chrysler small blocks and 245 265 Hemi 6 engines. However, one
of our major tools was sabotaged in 2003 to prevent us from releasing this new
supercharging technology which forced us to put the Hemi 6 Kits on hold. We also organised
a number of aftermarket manufacturers to produce or supply heavy duty high quality parts
for the Negative Supercharging Kits. This was required to keep the engines reliable with
the massive torque produced by Negative Pressure Supercharging.
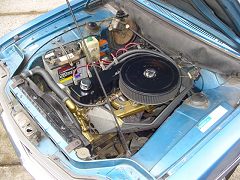
We approached a number of well known performance aftermarket manufacturers in the US to
set up Negative Supercharging Kits for the wide range of engines in the market. We offered
to demonstrate the massive torque and the many performance improvements produced by a 360
Chrysler small block fitted with the Negative Pressure Supercharging process.
Unfortunately, the performance aftermarket manufacturers were
not interested to see our 360
prototype engine because they figured this new supercharging
technology is so radical it couldn't possibly work.
This had no bearing on the viability of the Negative
Pressure Supercharging technology. Instead it reflects
the narrow-minded attitude of today's automotive engineers
who have become so familiar with the operating principles
of the 4-stroke engine, they refuse to accept any new
technology that works outside the square.
This was a disappointing setback to making Negative Supercharging Kits available for the
wide range of engines in the market. But at the same time we were flattered that the
Negative Pressure Supercharging process is so highly advanced it works beyond the
comprehension of the greatest minds in the automotive industry. Despite this obstacle we
continued to set up Negative Supercharging Kits for Chrysler small blocks.
Top of page
2003-2004 Tooling Up to Production
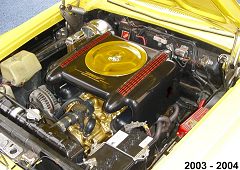
Negative Supercharging Kits were scheduled to be introduced in March 2003 for initially
318 360 Chrysler small blocks. All the tooling was completed and over 100 Negative
Supercharging Kits were produced. However, we were not able to produce the Thermocharger
air cleaner housing which prevented us from releasing the Kits.
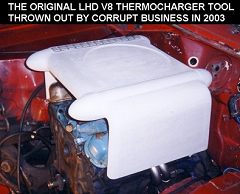
This was due to a corrupt business that sabotaged the Negative Supercharging Kits by
intentionally throwing out our Thermocharger tooling to prevent us from releasing this new
supercharging technology. This unfortunate event set us back 2 years. The photos show one
of only 3 original LHD Thermochargers produced before they threw out the tooling. The
original RHD Thermocharger never made it to production. We had no choice but to start
again from scratch and set up the new tooling for the LHD and RHD Thermocharger so
Negative Supercharging Kits will be available in 2005 for Chrysler small blocks, left and
right hand drive vehicles and for other make of engines in the future.
Top of page
2005 Production
Over the
past 17 years we invested millions and struggled to develop the complex process of the
Negative Pressure Supercharging technology using are own resources and with no financial
help from investors or government funding. We also used our own resources to set up the
tooling to produce Negative Supercharging Kits for 318 360 Chrysler small blocks.
Therefore, we are proud to introduce Negative Pressure Supercharging for the first time
this year as a revolutionary new technology that makes the engine supercharge itself using
NO air pump and the technology was financed and developed exclusively by Impulse Engine
Technology P/L in Australia.
Negative Supercharging Kits will be available in 2005 for initially 318 360 Chrysler small
blocks. Kits for other Chrysler, GM and Ford 6 and V8 engines will be available in the
future. Negative Supercharging Kits are made in Australia.
Top of page
2007 Tooling Up for Other Engines
As Negative Supercharging Kits demonstrate their ability to transform engines into
powerful fuel efficient power plants that produce the violent acceleration of race cars
and the massive towing power of trucks, more people will become interested in the many
performance advantages of this new supercharging technology.
This may encourage the performance aftermarket manufacturers to produce Negative
Supercharging Kits for the many different make and size of engines in the market. However,
if this does not happen we will endeavor to set up Negative Supercharging Kits for 400 440
Chrysler big blocks, 245 265 Chrysler Hemi 6, 198 225 Chrysler Slant 6, 327 350 Chevy
small blocks and 302 351 Ford small blocks.
Top of page
2008 and the Future
In the future we plan to set up Negative Supercharging Kits for more applications that
include GM and Ford big blocks, Harley Davidson motorcycle engines, V8 inboard marine
engines and Continental or Lycoming propeller plane engines.
As more businesses take an interest in the performance advantages of this new
supercharging technology and set up Negative Supercharging Kits for the many different
engines in the market, Negative Pressure Supercharging will be available for a wider range
of engines in the future.
Negative Pressure Supercharging is set to become the engine technology of the
future for the following reasons:
- It's a highly advanced process that makes the engine supercharge itself using NO air
pump
- It combines the performance advantages of 3 different engines into one engine,
1) the violent acceleration of a race car,
2) the smooth idle and fuel economy of a family car, and
3) the massive towing power of a truck from idle
- It allows smaller engines of half the capacity to produce the same acceleration and
towing power as much larger engines while substantially improving fuel economy and
emissions
- It costs 1/3 the price of conventional supercharger or turbocharger air pump systems
- It can be easily applied to every car, pickup, RV, truck, bus, motorcycle, boat, tractor
to propeller plane engine produced from 1900-2007
Impulse Engine Technology
P/L |
PO Box 986 Randwick NSW 2031 Australia
Ph: (02) 9398 5544 Fax: (02) 9398 5644
International: Ph: +(612) 9398 5544 Fax: +(612) 9398 5644
Email Us
Inventor of Negative Pressure Supercharging
|
|